Evoluția tehnologiei de ungere verde de tăiere
Scopul tăierii lichidului
În timpul procesului de tăiere, temperaturile ridicate și presiunea ridicată sunt produse la partea de tăiere din cauza frecării severe, ceea ce afectează grav durata de viață a instrumentului, precizia și finisarea suprafeței părții prelucrate.
Există două măsuri principale pentru reducerea temperaturii, reducerea frecării, asigurarea duratei de viață a sculei și a preciziei piesei:
(1) reducerea frecării în timpul tăierii și reduce uzura sculei;
(2) Scoateți temperatura ridicată adunată în partea de tăiere în timp.
Metoda de ungere tradițională este de a pulveriza lichidul de tăiere până la punctul de prelucrare. Conform experienței, cu cât este mai mare furnizarea de lichid de tăiere, cu atât este mai bun efectul. În ultimii ani, „răcirea de înaltă presiune” a fost promovată activ în domeniul tăierii. Pentru o perioadă, o sursă mare de lichid de tăiere a fost considerată „salvatorul” tăierii.
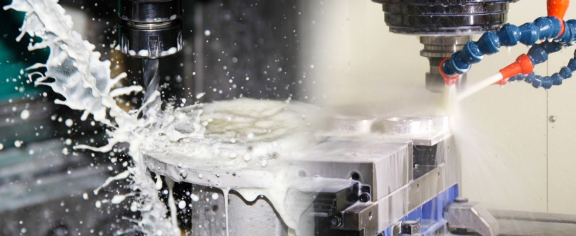
Pericole de utilizare a lichidului de tăiere Începând cu secolul XX, industria de fabricație a mașinilor a suferit noi schimbări: (1) Lumea a acordat o atenție pe scară largă problemelor de protecție a mediului, cum ar fi încălzirea globală, distrugerea stratului de ozon și generarea de dioxine; (2) îngrijorarea cu privire la pericolele pentru sănătate cauzate de aditivi din lichidul de tăiere operatorului și de pericolele de siguranță cauzate de scurgerea și dispersia agentului petrolier către operator; (3) Acordați atenție poluării mediului cauzate de tratarea petrolului rezidual, iar opinia publică cere cu tărie ca lichidul de tăiere să îndeplinească cerințele de protecție a mediului.
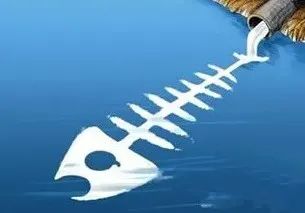
În acest context, țările europene și americane și Japonia au formulat sau revizuit Legea privind tratarea uleiului rezidual, legea înregistrării mobile pentru emisia de poluanți de mediu și legea specială pentru tratamentul dioxinei. Drept urmare, deși o cantitate mare de lichid de tăiere poate primi o mai bună lubrifiere, o calitate mai mare a calității de procesare și eficiența procesării, în conformitate cu cerințele protecției mediului, deșeurile de tăiere trebuie tratate nevinovat înainte de a putea fi descărcate. Noile cerințe au crescut mult costul tăierii. Conform sondajului unei fabrici de automobile germane, costul instrumentului reprezintă 2% ~ 4% din costul total de producție; Costul legat de reducerea lichidului reprezintă 7%~ 17%, care este de 3 ~ 5 ori din costul instrumentului. Principala rotație a arborelui reprezintă 20% din consumul de energie al atelierului de prelucrare, în timp ce consumul de energie legat de răcire reprezintă 53%. Pentru a rezuma, utilizarea necontrolată a lichidului de răcire pentru a reduce consumul de instrumente și energie poate fi contraproductivă. Tehnologia de ungere modernă 1. Metoda de tăiere uscată Tăierea uscată fără lichid de tăiere poate rezolva complet problemele de mediu cauzate de tăierea lichidului. În ultimii ani, odată cu dezvoltarea rapidă a materialelor de scule, temperatura de tăiere adaptabilă a crescut semnificativ.
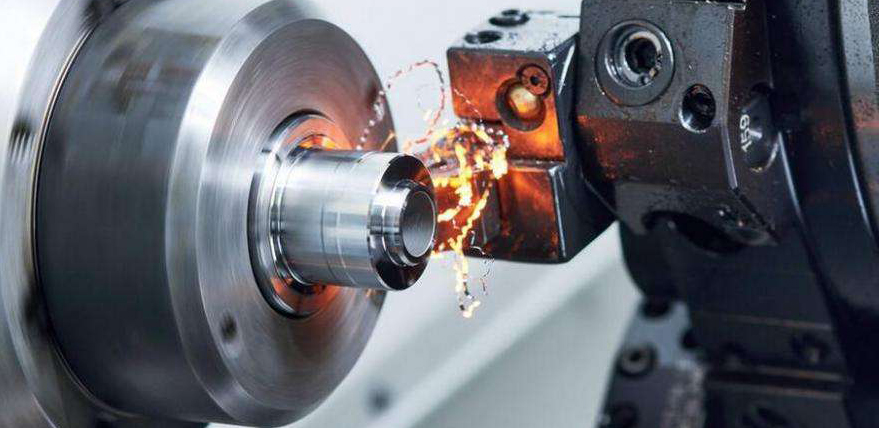
Instrumentele tradiționale din oțel cu unelte au o temperatură rezistentă la căldură între 200 și 300 ℃. Dincolo de această temperatură, duritatea instrumentelor va scădea semnificativ, iar instrumentele vor fi purtate rapid și aruncate. Instrument de oțel de mare viteză, temperatura maximă admisă poate atinge 500 ~ 600 ℃; Temperatura de tăiere a instrumentelor cu diamante poate ajunge la 800 ℃ (deoarece coeficientul de frecare a instrumentelor cu diamante este foarte scăzut și nu poate fi utilizat pentru tăierea metalelor feroase, temperatura este scăzută). Instrumentul compus dur poate încă tăia la 800 ~ 1000 ℃; Instrumentele ceramice pot fi utilizate la 1200 ℃; Temperatura de service a instrumentului de nitrură cubic de bor poate ajunge la 1400 ℃. Metoda de procesare, performanța instrumentului și materialul care trebuie procesat sunt bine potrivite, iar tăierea uscată este cea mai simplă metodă de procesare. Cu toate acestea, deoarece tăierea uscată nu folosește lichidul de tăiere, coeficientul de frecare este mare, rezistența la tăiere este mare, iar eficiența este scăzută; În plus, căldura generată în procesul de tăiere nu poate fi schimbată la timp, ceea ce duce la creșterea problemelor de suprafață ale instrumentului și a piesei de lucru, iar piesa de lucru nu este ușor de obținut o precizie ridicată. 2. Metoda de tăiere MQL Metoda ideală este să utilizați cantitatea minimă de lubrifiant pe premisa de a asigura lubrifierea și performanța de răcire și îndeplinirea cerințelor de protecție a mediului. Această metodă de procesare se numește tăiere semi-uscată.
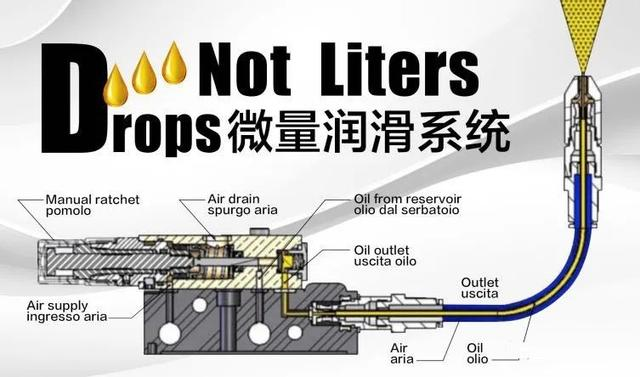
Pentru tăierea semi-uscată, furnizarea de lichid de tăiere este mică, ceea ce necesită ca lichidul de tăiere să fie adăugat în partea de tăiere practic și fiabil. Se pare că irigarea agricolă s -a dezvoltat din irigarea inundațiilor până la irigarea stropită și apoi la irigarea prin picurare. O cantitate mică de apă este turnată direct pe rădăcinile culturilor.
În ultimii ani, tehnicienii de ungere au dezvoltat o serie de noi metode de semi-tăiere pentru protecția mediului, conservarea energiei și eficiența ridicată. De exemplu, metoda de prelucrare MQL, metoda duzei plutitoare, metoda de răcire megasonică și tehnologia lor de tăiere semi-uscată și îmbunătățită și compusă. În prezent, metoda de procesare recent dezvoltată MQL (Minim Cantitate Lubrifiants) a dus la modificări de epocă în tehnologia de lubrifiere. Structura tipică a lubrifierii MQL este prezentată în figura de mai jos.
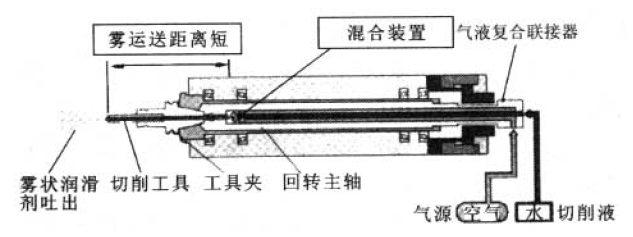
Structura este compusă din axul de mașini -unelte, sistemul de alimentare cu ulei și sistemul de alimentare cu aer. În fusul gol, este plasat un mânecă, tubul interior este umplut cu ulei, iar tubul exterior este ventilat. Uleiul și gazul sunt amestecate de dispozitivul de amestecare de la capătul frontal al fusului, iar lubrifiantul de ceață este introdus la instrumentul de tăiere. Deoarece partea rotativă a lubrifiantului de ceață este foarte scurtă, aceasta nu este afectată de forța centrifugă. Lubrifiantul de ceață este pulverizat eficient prin gaura din fața sculei și pulverizată cu exactitate până la partea de tăiere. Pompa cantitativă pentru alimentarea cu ulei este controlată de CNC (compus numerical Contr01), iar cantitatea de alimentare cu ulei poate fi setată în mod arbitrar. Alimentarea cu combustibil a sistemului MQL nu este mai mare de 50 ml/h; Presiunea de gaz comprimată este de 0,2 ~ 0,4MPa. Procesarea MQL are o serie de avantaje: (1) Consumul de ulei este mic, doar 1/20 ~ 1/5 din metoda tradițională. (2) Nu există aproape niciun ulei pe cip. (3) Există un pic de ulei atașat la piesa de prelucrat, care poate simplifica procesul de curățare a piesei. (4) Sistemul de circulație a lichidului de răcire care consumă multă energie este eliminat. (5) Nu este necesară o gestionare complexă a ungerii. (6) Este convenabil să instalați sistemul MQL pe mașinile -unelte existente. Conform cerințelor de protecție a mediului și caracteristicile unei bune performanțe lubrifiante și durata de viață lungă a uleiului cerut de următoarea generație de mașini -unelte, ungerea MQL ar trebui să utilizeze ulei de lubrifiere ester cu o bună biodegradabilitate, capacitate ridicată de rulment, pierdere scăzută de evaporare și excelent Stabilitatea oxidării. Utilizarea uleiului de ester în metoda de ungere a MQL poate rezolva problemele de performanță a lubrifierii și protecția mediului. Cu toate acestea, efectul de răcire nu este suficient doar prin aer comprimat, astfel încât au fost dezvoltate unele metode de ungere îmbunătățite MQL. De exemplu, după atomizarea uleiului și respectiv a apei, pulverizați -le până la punctul de tăiere în același timp într -o anumită proporție. În plus, „Metoda de cădere a apei cu film de ulei”, adică uleiul, apa și aerul sunt furnizate simultan prin carcasă cu mai multe straturi, astfel încât un strat de peliculă este atașat la suprafața căderii de apă și pulverizat la procesare parte sub forma de ceață. Căldura este luată de evaporarea picăturii de apă pentru răcire, iar filmul de ulei rămas este utilizat pentru lubrifierea și prevenirea ruginii. 3. Alte metode de micro-lubrifiere Există, de asemenea, metoda duzei plutitoare și metoda de răcire megasonică (Megasonic CDOLANF) pentru procesul de măcinare.